History
Search
1986-1990 Hobby shop
The 1st room (20 mē): The sales office
The growth of the business could be seen from the sales counter. The old abandoned wooden table that was used in the first years was now replaced, after three years, with a proper counter made of fibreboard. After 7 years, the first financial successes meant that the sales office could be made brighter and more attractive.
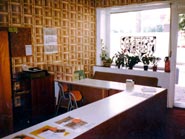
The shop was now open 7 hours per week, not forgetting overtime in the evenings and programming hours through the night.
"Unfortunately" there was less and less time left to study. And when the first companies had some boards made, such as Siemens and the Hahn-Meitner Institute, the owner's pride was immense. This was associated with the worry, that the companies would discover that they were producing with home made equipment. Surprisingly, this wasn't too important for the developers.
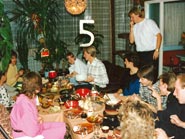
A "computer" helped to produce the invoices.
At the time, all of the software had been developed and programmed by Andreas Contag himself. Initially, it was a Commodore VC20 with 0.02 MB of memory, which was then replaced by a C64 with a daisy-wheel typewriter attached.
When the Atari ST then came on to the market, all of the software had to be rewritten in months of work at night.
The 2nd room (20 mē): Production
Production proceeded as follows:
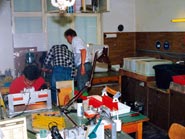
2. Expose: The transparent film was placed on the base material coated with photosensitive varnish, fixed with paper clips and exposed for 3 minutes to ultraviolet light produced by a plant lamp.
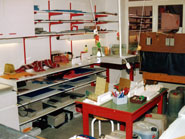
4. Drill: The following game supplied the motivation: Four students (both Contags and two helping friends) sat around a table, each with a small hand drill. "Ready, steady, go": The winner was the first one to completely drill 10 boards (about 1000 holes). Shame on the one who misplaced even just one hole ... quality was always very important!
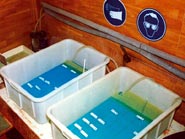
First expansion! Renting the adjacent flat
In 1989, it became necessary to expand. The flat next door was the obvious choice, but at the time it was still rented out. Once the occupant had been found a new flat, there was nothing standing in the way of expansion to 120 square metres.
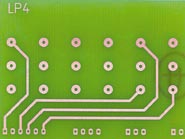
Through the expansion, there was finally a toilet of their own. There was even a small conference and break room, where a wooden board installed by the previous tenant served as storage space.
Printed circuit board technology
The product spectrum
- Single-side circuit boards
- Double-sided circuit boards, but without chemically deposited through contacts
- Minimum track width: 1.0 mm
- Smallest diameter hole: 0.8 mm
Your personal contact
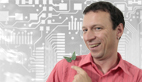
Guido Strehl
Assistant to the general
manager
+49 30 351 788-225
guido.strehlcontag.de